Cork underlay is often used under wood floors for several reasons. A cork underlay may be required or recommended in the following situations:
Acoustic insulation: Cork perfectly dampens sound, which is especially important in multi-story buildings where noise reduction is crucial for the comfort of the residents.
Thermal insulation: Cork has good insulating properties that can help keep the room warm, especially if the floor is above an unheated room or on the ground.
Surface leveling: A cork underlay can help level out minor unevenness in the subfloor, which is important to ensure the stability and durability of a wood floor.
Moisture protection: Although cork alone is not completely waterproof, it can help protect your wood floor from moisture, especially when used in conjunction with other insulating materials.
Underfoot comfort: Cork is soft and flexible, which makes the wood floor more comfortable to use.
When is a cork underlay required?
Floating floors: When installing a floating floor (planks are laid without being firmly attached to the floor), a cork underlay is often recommended to improve comfort and reduce noise.
Old subfloors: When installing a wooden floor on old, uneven subfloors, a cork underlay can help to level the surface.
Floors above living spaces: In residential buildings where wooden floors are installed above other living spaces, a cork underlay can significantly reduce sound transmission.
How to choose a cork underlay?
When choosing a cork underlay, it is worth paying attention to its thickness (usually 2 to 6 mm) and density, which affects its insulating and acoustic properties. It is also important that the underlay is suitable for the type of wooden floor and its installation method.
In summary, a cork underlay is required or recommended in many situations to ensure the comfort, durability and insulation of a wooden floor.
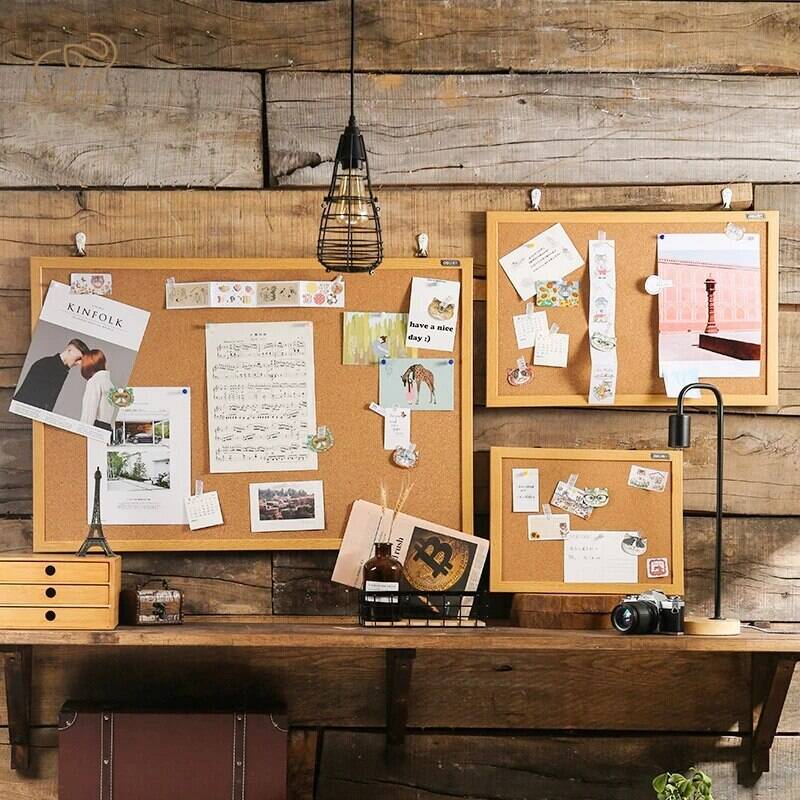
Production of cork underlayment
Cork underlay is made from the bark of the cork oak (Quercus suber), which has unique insulating and acoustic properties. The production process of cork underlay can be divided into several stages:
Bark harvest:
The bark of the cork oak is harvested every 9-12 years in a way that does not damage the tree.
The bark is harvested by hand to ensure its high quality.
Drying:
The collected bark is air-dried for several months, which removes excess moisture and stabilizes the material.
Grinding and granulating:
The dry bark is ground into fine cork granules.
The granules are then sieved and sorted by size.
Pressing and forming:
Cork granules are compressed under high pressure, often with the addition of a small amount of glue, to create cork slabs.
The boards are formed into appropriate shapes and thicknesses.
Final processing:
Cork boards can be subjected to further processing, such as cutting to appropriate dimensions, sanding and packaging.
How to store a cork foundation
To ensure that the properties of the cork underlay are preserved, it is important to store it properly:
Environmental conditions:
Store the primer in a dry, well-ventilated place, away from sources of moisture.
The room temperature should be stable, preferably between 15°C and 25°C.
Avoid direct sunlight, which may lead to degradation of the material.
Stacking and storage:
Store cork boards on a flat surface to avoid deformation.
If you are storing large amounts of underlayment, stack the boards, but do not exceed the recommended stack height so as not to cause excessive pressure on the bottom boards.
Keep the original packaging if possible to protect the discs from dust and mechanical damage.
Protection against pollution:
Avoid contact of the primer with chemical substances that may damage the material.
Protect the boards from dust and dirt to maintain their insulating and acoustic properties.
Additional tips
Before using the cork underlay, it is worth acclimatizing it in the room where it will be installed for at least 48 hours. This will allow the material to adapt to the conditions in the room.
Regularly check the condition of your stored foundation to make sure it is not damaged or contaminated.
Following these recommendations will help keep your cork underlayment in perfect condition and ensure its long-term effectiveness as a wood flooring material.
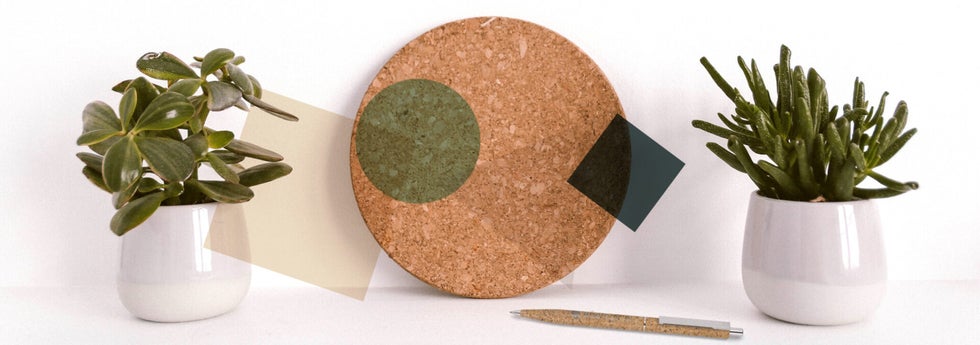
Cork boards are a popular and practical solution for hanging notes, photos and other materials. The cork underlay used to produce cork boards is slightly different from the underlay used for wooden floors. Here's how the production and use of cork backing in cork boards looks like:
Production of cork base for cork boards
The production process of cork underlay for cork boards is similar to the production of floor underlays, but with some differences:
Bark harvest:
The bark of the cork oak is harvested every 9-12 years.
Harvesting is done manually to ensure high quality of the raw material.
Drying:
The bark is air-dried for several months.
Grinding and granulating:
The bark is ground into fine granules.
The granules are sorted by size.
Pressing and forming:
The granules are pressed under high pressure, often with a small amount of glue added, to create cork boards.
The boards are formed into appropriate shapes and thicknesses, often thinner than floor underlays.
Final processing:
Cork boards are cut to appropriate dimensions.
The surface can be additionally smoothed and finished to make it aesthetic and functional as a board.
The use of cork underlay in cork boards
Cork backing in cork boards is selected due to its properties:
Flexibility and density:
The cork is flexible enough to easily stick tacks or pins into it, and at the same time dense enough to keep them in place.
Durability:
Cork is a durable material, resistant to mechanical damage, which means that cork boards can be used for a long time without visible signs of wear.
Sound insulation:
Cork boards can also act as sound insulation, which is useful in offices and public places.
Storing cork backing for cork boards
Cork backing intended for cork boards should be stored in appropriate conditions to maintain its properties:
Environmental conditions:
Store in a dry, well-ventilated place.
Avoid direct sunlight and excessive moisture.
Stacking and storage:
Store cork boards on a flat surface.
Avoid stacking large piles to avoid deformation.
Protection against pollution:
Avoid contact with chemical substances.
Protect against dust and dirt.
Additional tips
If you plan to use cork backing to make your own cork boards, make sure you have the appropriate cutting and assembly tools.
The cork can be glued to various surfaces, such as wood, metal or plastic, using appropriate mounting adhesives.
Cork boards are a practical and aesthetic solution, and the appropriate cork backing ensures their durability and functionality.